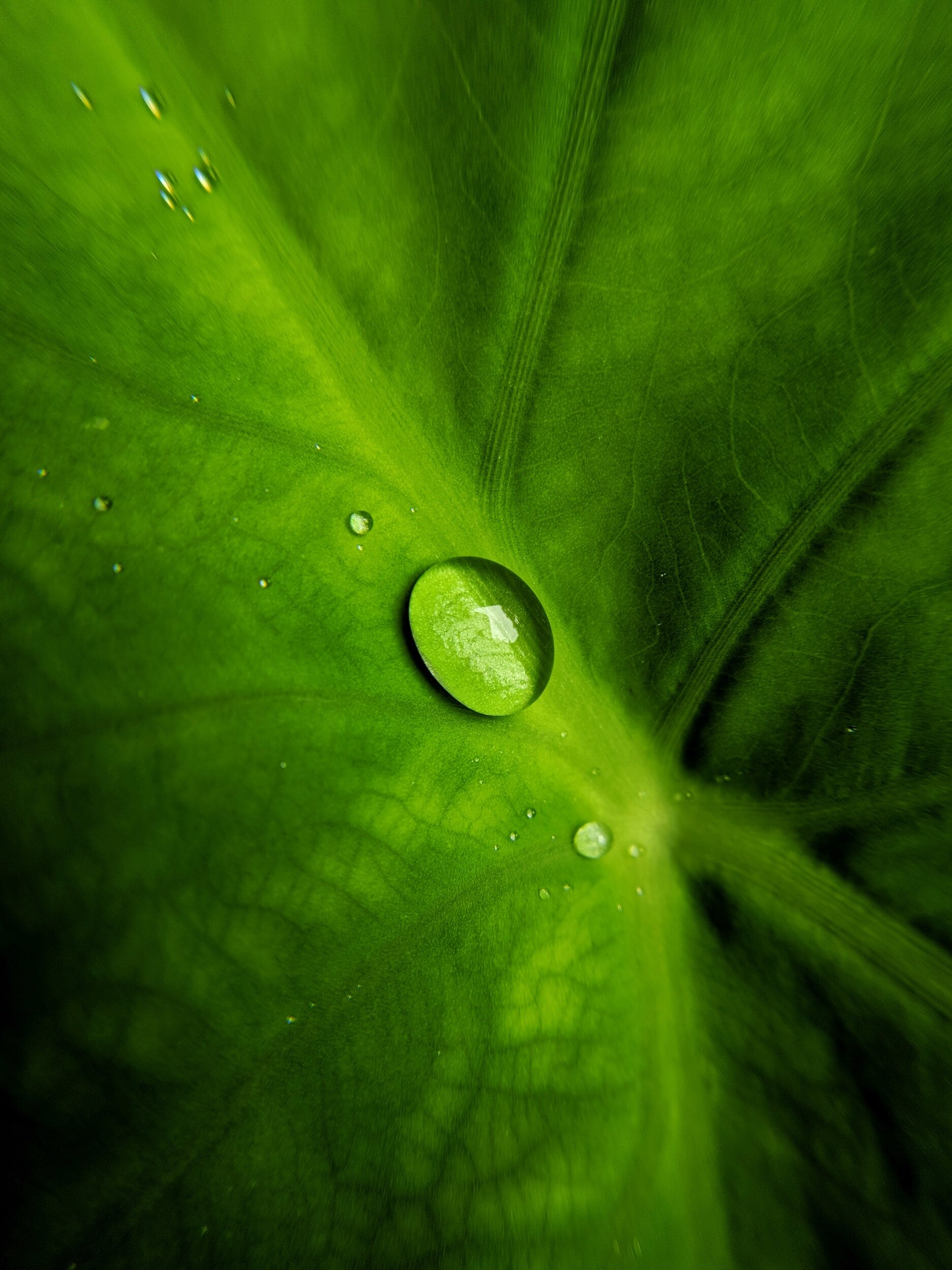
Green Hydrogen
Hydrogen
Welcome to the heart of Hydrogen innovation at Superior Brands Corp., where our commitment to advancing technology encompasses two core competencies: Hydrogen and Solar Power. As leading manufacturers, we take you on a journey through the transformative landscape of Hydrogen production, redefining the way energy is harnessed, stored, and utilized.
-
Harnessing the Power of Water
Within the realm of Hydrogen production, a symphony of technologies orchestrates the separation of hydrogen from water, each unlocking a distinct potential. Electrolysis, photolysis/photonic hydrogen separation, and direct solar water splitting are among the top technologies currently available. Electrolysis is currently the only option commercially available, although the other technologies are starting to show more promise.
-
Electrolysis: A Time-Honored Pioneer
Among these technologies, electrolysis stands above all else – a trailblazer that has been transforming the energy landscape for generations. In this intricate process, a solution of water with a cathode and an anode immersed forms the foundation. The application of electricity triggers the molecular dance within H2O, breaking bonds and yielding the liberation of O2 and 2H2 molecules. The Hydrogen gravitates to one side, while oxygen is drawn to the other, often facilitated by a membrane. The process of electrolysis does not produce any greenhouse gas, making this process one of the cleanest forms of energy currently available. When electricity from renewable sources, like the solar panels Superior Renewable Corp. manufacturers, is used the hydrogen produced is considered green hydrogen.
-
Efficiency in Kilowatt Hours per Kilogram
At the heart of Hydrogen production lies the quest for efficiency. Hydrogen producers measure success by the ratio of electric energy, expressed in kilowatt hours (kWh), consumed to produce 1 kilogram of hydrogen – a metric known as kWh/kg. This process essentially converts water and electric power into hydrogen and oxygen. A lower electric input per 1kg of H2 signifies a more efficient process.
-
Two Pillars of Efficiency: Low-Temperature and High-Temperature Electrolysis
In the world of electrolysis, two titans emerge: low-temperature electrolysis (LTE) and high-temperature electrolysis (HTE). Both methods harness the power of an electric current to separate water molecules into hydrogen and oxygen. While LTE serves various applications with its widespread deployment, HTE takes the stage with higher efficiency and the promise of integration with high-temperature heat sources.
-
Low-Temperature Electrolysis (LTE): The Tried and True Path
Within the hydrogen landscape, LTE emerges as the most familiar and widely adopted pathway. Often referred to as conventional electrolysis, LTE operates at moderate temperatures, typically ranging from room temperature (20 degrees Celsius) to approximately 90 degrees Celsius. At the heart of this process lies the electrolyzer device, a cornerstone in transforming water into its constituent elements.
-
The Dance of Water Molecules
The electrolyzer boasts two pivotal components – an anode and a cathode – immersed within an electrolyte solution. This solution, typically a blend of water and added electrolyte substances like potassium hydroxide or sulfuric acid, sets the stage for a molecular symphony. When an electric current gracefully sweeps across the electrodes, water molecules (H2O) surrender to the rhythm, fragmenting into their elemental dance partners: hydrogen (H2) gravitates towards the cathode, while oxygen (O2) elegantly finds its place at the anode.
-
The Power of Direct Current
LTE thrives on direct current (DC) electricity sourced from external power outlets. Whether renewable power is harnessed from solar panels or drawn from the grid, this electricity breathes life into the electrolyzer, initiating the intricate ballet of water molecule dissection.
-
A Sustainable Future Beckons
Low-temperature electrolysis stands as a testament to the enduring legacy of innovation and sustainability. As Superior Renewable Corp. explores the frontiers of hydrogen technology, we embrace the significance of LTE as a critical step towards cleaner energy landscapes. With every hydrogen molecule liberated, we take strides toward a greener and more promising tomorrow, one where hydrogen reigns as a beacon of possibility and progress.
-
High-Temperature Electrolysis (HTE): Forging New Horizons
Beyond the familiar shores of LTE lies high-temperature electrolysis (HTE), a more advanced and nuanced approach to harnessing the power of hydrogen. With temperatures ascending to remarkable heights – typically ranging between 700 to 1,000 degrees Celsius – HTE orchestrates a symphony of innovation that holds the promise of unprecedented efficiency and remarkable progress.
-
Solid Oxide Electrolysis Cells and Proton-Conducting Ceramics: The Building Blocks of HTE
Central to the HTE narrative are the solid oxide electrolysis cells (SOECs) and proton-conducting ceramic electrolytes. These remarkable components constitute the essence of an electrolyzer device primed for operation at elevated temperatures. The intensified thermal environment not only accommodates these novel materials but also accelerates the kinetics of the electrolysis reaction, ushering in efficiency on an unprecedented scale.
-
The Marriage of Heat and Energy: A Kinetic Partnership
At its core, HTE stands as a testament to the harmonious fusion of thermal energy and electrical generation. This advanced process integrates seamlessly with high-temperature heat sources, ranging from concentrated solar power to nuclear reactors, waste heat from petroleum refineries, ammonia producing factories, and even steel manufacturing plants. Through the utilization of surplus or waste heat, HTE achieves a remarkable feat – higher overall energy efficiency when compared to its low-temperature counterpart.
-
Gibbs Free Energy: Unleashing Potential at Elevated Temperatures
Driving the elegance of HTE is the fundamental principle of Gibbs Free Energy – the work required to dismantle a water molecule into its elemental constituents (Hydrogen and Oxygen gas) diminishes with the surge in inlet water temperature. This tenet serves as the bedrock of high-temperature electrolysis, facilitating a transformative energy conversion process that aligns seamlessly with concentrated solar power (CSP) operations.
-
A Symphony of Possibilities: Crafting a Green Energy Symphony
The marriage of high-temperature electrolysis with CSP paints an emblem of a truly sustainable future. Within the realm of HTE, true green electricity takes center stage, where residual waste steam from the heat recovery steam generator (HRSG) plays a vital role in elevating overall system efficiency. This synergy embodies the pinnacle of innovation, where renewable energy sources synchronize with waste utilization, driving progress and painting a portrait of a cleaner, greener energy landscape.
As Superior Renewable Corp. ventures deeper into the realm of hydrogen technology, we embrace the transformative potentials of high-temperature electrolysis. With HTE as our guiding light, we carve a path towards a more sustainable future, where energy efficiency and innovation coalesce to illuminate a world fueled by progress and possibility.
As manufacturers at the forefront of Hydrogen technology, Superior Renewable Corp. is poised to redefine energy possibilities. Our commitment to innovation, sustainability, and efficiency echoes through every process, propelling us forward on a journey that ushers in a new era of clean and sustainable energy carriers.
-
Unleashing the Power of Hydrogen
With Hydrogen and Solar Power as our compass, we navigate the seas of energy transformation. As a pioneering force, Superior Renewable Corp. is dedicated to shaping a future where Hydrogen takes center stage, driving progress and innovation that resonate with a cleaner, greener, and more sustainable world. Join us as we dive into the hydrogen landscape, where innovation meets aspiration and energy finds new dimensions.
Alkaline Electrolysis
Alkaline electrolysis stands as the significant vanguard in the realm of hydrogen production. At Superior Renewable Corp., we're at the forefront of manufacturing cutting-edge alkaline electrolysis systems that harness the power of electrochemical reactions to produce clean and sustainable hydrogen gas. This technology is an integral part of our commitment to advancing the green energy landscape and fostering a more sustainable future.
-
Unlocking Hydrogen Potential through Alkaline Electrolysis
At the core of alkaline electrolysis lies a remarkable process that converts water into hydrogen and oxygen gases using electricity in an alkaline environment. In our systems, two electrodes submerged in a liquid alkaline electrolyte solution, usually potassium hydroxide (KOH), play a pivotal role. These electrodes, one negatively charged and the other positively charged, are separated by a porous diaphragm. This diaphragm ensures the separation of the hydrogen and oxygen gases, allowing for efficient collection.
The process commences as water undergoes decomposition at the cathode. Four water molecules gain four electrons, transforming into two molecules of hydrogen (2H2) and four hydroxide ions (4OH-). These hydroxide ions migrate through the solution to the anode, completing the circuit. At the cathode, the hydroxide ions release four electrons, resulting in the formation of two water molecules (2H2O) and one molecule of oxygen gas (O2).
-
Alkaline Electrolysis: Efficiency, Reliability, and Versatility
Our alkaline electrolysis systems exemplify efficiency, reliability, and cost-effectiveness. Notably, these systems offer the most cost-effective means of producing significant quantities of hydrogen. They exhibit a slow rate of degradation, roughly half that of PEM electrolyzers, and boast an operational life of around 90,000 hours before major maintenance is required. It's important to note that alkaline electrolyzers require a protective current for equipment preservation, making them better suited for applications connected to stable power grids rather than direct integration with renewable energy sources.
-
Embracing the Power of Alkaline Electrolysis
Alkaline electrolysis finds its strength in large-scale centralized hydrogen plants, fitting perfectly into a hub-and-spoke distribution network. Our turnkey alkaline hydrogen plants comprise essential components:
• Electrolyzer Stacks: These stacks, containing multiple cells of anodes and cathodes separated by electrolytes, serve as the heart of the system. The water-splitting reaction occurs here, producing hydrogen and oxygen gases.
• Power Supply: A power supply provides the necessary electrical energy to drive the electrolysis process. It converts incoming electrical power into the appropriate voltage and current required by the electrolyzer stack.
• Gas-Lye Treater: This component manages the mixture of hydrogen-rich and oxygen-rich lye from the electrolyzers, sending lye back for further electrolysis. It separates and cleans gases for further treatment.
• Cooling System: Electrolysis generates heat, necessitating a cooling system to maintain operational temperatures. Cooling mediums ensure optimal performance and system longevity.
• Gas Separation and Collection: Gas separation membranes or methods ensure that collected hydrogen gas is produced pure, collected at the cathode side, while oxygen gas is collected at the anode side.
• Pressure Regulation and Storage: Pressure regulators and storage equipment increase hydrogen gas pressure for effective storage and utilization.
-
Empowering a Hydrogen-Powered Future
Superior Renewable Corp. is your partner in harnessing the potential of alkaline electrolysis. Our turnkey hydrogen plants, equipped with cutting-edge alkaline electrolysis systems, offer the equipment required for efficient, clean, and reliable hydrogen production. As we continue to lead the way in green energy solutions, our commitment to a sustainable and eco-friendly future remains unwavering.
PEM Electrolysis
Proton Exchange Membrane (PEM) electrolysis is an upgraded form of low temperature electrolysis that has revolutionized the hydrogen production process by replacing the traditional alkaline solution with a solid polymer electrolyte membrane. At Superior Brands Corp., we specialize in delivering cutting-edge PEM electrolyzer systems that pave the way for efficient and sustainable hydrogen generation.
-
Advancements Beyond Alkaline Electrolysis
PEM electrolysis represents a significant advancement from conventional alkaline electrolysis. The key innovation lies in replacing the alkaline solution and diaphragm with a solid polymer electrolyte membrane. Part of the safety features of alkaline come from the distance between the cathode and the anode. In PEM technology hydrogen and oxygen do not bubble up in the same fashion around the electrodes and therefore do not need the same separation. PEM technology does not use an alkaline solution and therefore does not need a reservoir or lye treatment to recycle the alkaline solution back into the electrolyzer. This frees up the design to be far more compact. This design overhaul offers numerous benefits, including enhanced efficiency, compact footprint, and rapid ramp-up and ramp-down capabilities.
-
The Chemistry of PEM Electrolysis
Within a PEM electrolyzer, the electrochemical reactions unfold in a different manner compared to alkaline electrolysis. Water splitting occurs at the anode, where two water molecules release four electrons to form an oxygen molecule and four protons (H+ ions). These protons traverse the solid polymer electrolyte membrane to reach the cathode, where they combine with four electrons to yield two hydrogen molecules.
In this operation, the solid polymer membrane acts as a dual-function component, serving as both the electrolyte solution and the diaphragm membrane found in alkaline electrolysis technology. This innovative membrane facilitates the separation of oxygen and hydrogen gases while enabling the proton conduction essential for the electrochemical reactions.
-
Advantages of PEM Electrolysis
PEM electrolyzers offer distinct advantages over their alkaline counterparts. With higher efficiency and a more compact design, PEM electrolyzers are ideal for applications where space is limited. However, they degrade at a faster rate than alkaline electrolyzers, typically requiring maintenance after around 40,000 hours of operation.
This dynamic technology boasts rapid ramp-up and ramp-down capabilities and can efficiently operate across a wide capacity range of 0-100%, making it well-suited for applications directly connected to renewable generation sites, such as solar farms.
-
Main Components of PEM Electrolysis
Our PEM electrolyzer systems consist of several critical components, working harmoniously to ensure efficient hydrogen production:
• Electrolysis Stack: The core of the PEM electrolyzer is the stack, housing multiple cells in a bipolar plate assembly. Each cell features an anode and cathode separated by a solid polymer electrolyte membrane. The stack is where the hydrogen and oxygen gases are produced.
• Cooling System: To regulate temperature and prevent overheating, PEM electrolyzers require a robust cooling system. Water or other cooling fluids effectively dissipate generated heat, maintaining optimal operating conditions.
• Gas Separation and Collection: Efficient separation and collection of hydrogen and oxygen gases are achieved through various techniques, including pressure differentials, gas diffusion layers, and collection channels. Similar to gas separation in Alkaline, this is where any trace oxygen is removed from the product hydrogen.
• Pressure Regulation and Storage: The hydrogen gas generated by PEM electrolysis is typically at low pressure. Pressure regulation and storage equipment, such as compressors and storage tanks, elevate gas pressure for storage or further utilization.
• Power Supply: The electrolysis process necessitates electrical energy. A power supply converts incoming electrical power into the specific voltage and current required by the electrolyzer stack. This is usually comprised of a step-down transformer isolation devices like circuit breakers, and an AC to DC power rectifier.
• Water Management System: Precise control of water content within the solid polymer electrolyte membrane is vital for optimal PEM electrolyzer performance. A sophisticated water management system maintains appropriate membrane hydration levels, preventing drying or flooding.
At Superior Brands Corp., we take pride in offering state-of-the-art PEM electrolyzer systems, supplying turn-key solutions encompassing all essential equipment components. Our dedication to sustainable and innovative green energy solutions drives us to deliver cutting-edge technology for a cleaner future. Explore the future of hydrogen generation through our PEM electrolyzer solutions that redefine the boundaries of efficiency, performance, and environmental stewardship.
Solid Oxide Electrolysis Cells (SOEC)
Superior Brands Corp. is a leading high temperature electrolysis solution based on oxide cells. The electrolyzer uses steam as a water feedstock instead of liquid water to produce hydrogen. Intelligently integrating hydrogen production with waste heat from industrial processes drastically reduces renewable energy electric demand for operating the electrolyzer.
-
SOEC Electrolysis: Pioneering the most efficient Green Hydrogen
SOEC feeds water into the cathode and the water undergoes water reduction reaction (WRR), which converts water into hydrogen gas and oxide ions. This hydrogen gas is later brought to purification modules to separate hydrogen gas from the remaining water. Then, the oxide ions migrate from cathode to anode, and they release electrons to external circuit to become oxygen gas via oxygen evolution reaction (OER). Typically, the operating temperatures for SOECs are from 700 to 1,000 °C, because high temperatures are required to thermally activate the migration of oxide ions and to facilitate electrochemical reactions on both electrodes. As a result, overall efficiency is improved.
-
Applications
This type of electrolyzer introduces the need for a high heat source that allows steam feedstock water to enter the inlet of the stack at degrees exceeding 150 °C. SOECs are ideal when paired with industrial consumers of hydrogen such as in oil refineries, steel manufacturing, and chemicals like fertilizer and ammonia production.
The components that make us SOEC balance of plant (BoP) are as follows:
• Water Treatment System (Reverse Osmosis and Electro-Deionizer): Before entering the SOEC stack, water needs to undergo thorough treatment to ensure it meets the purity requirements for efficient electrolysis. The water treatment system typically includes:
o Reverse Osmosis (RO): This process removes contaminants, ions, and impurities from the water by pushing it through a semipermeable membrane. RO helps achieve a high level of water purity by effectively filtering out dissolved solids and minerals.
o Electro-Deionizer (EDI): Electro-deionization further purifies the water by using an electric field to remove any remaining ions and impurities that may have escaped the RO process. This step ensures the water is highly purified and suitable for SOEC electrolysis.
• Heat Source Preparation: Water needs to be heated before entering the SOEC stack to facilitate the electrolysis process. A heat source, which can vary depending on the specific SOEC plant design, is essential to bring the water to the required temperature for efficient electrolysis. Common heat sources include:
o Industrial heat recovery steam generators (HRSG) Steam: Utilizing steam generated from external heat sources, such as concentrated solar power, waste heat from industrial processes, like refineries or ammonia production, to bring the water to the necessary temperature.
o Electric Heaters: Electrical heaters can also be used to heat the water to the desired temperature before it enters the SOEC stack.
• Solid Oxide Electrolyzer Cell (SOEC) Stack: The heart of the SOEC plant is the SOEC stack, where the actual electrolysis process takes place. The SOEC stack consists of multiple individual SOEC cells connected in series or parallel arrangements to achieve the desired hydrogen production capacity. Each SOEC cell comprises several layers, including an anode, electrolyte, and cathode. The high-temperature operation of SOECs allows for the electrolysis of steam, producing hydrogen gas and oxygen ions.
• Gas Separation and Collection: The SOEC stack produces hydrogen gas at the cathode and oxygen ions at the anode. Efficient separation and collection of the generated gases are crucial to ensure high-purity hydrogen output. Unlike Alkaline or PEM, the only impurities in the product hydrogen line are residual H2O molecules and any trace noble gases that were present in the inlet water vapor. Because there is no Oxygen in the output hydrogen there is no need for a deoxo. This means that SOEC plants only need compression and drying to knock out any water in the hydrogen.
• Pressure Regulation and Storage: The hydrogen gas produced by the SOEC stack is typically at a low pressure nearing 0 bar(g). Pressure regulation and storage equipment, such as large multi-staged compressors and storage tanks, are used to elevate the gas pressure to appropriate levels for storage or further utilization.
In summary, a comprehensive Solid Oxide Electrolyzer Cell (SOEC) plant includes water treatment systems such as reverse osmosis and electro-deionization to ensure high-purity water, a heat source to bring water to the required temperature, the SOEC stack for the electrolysis process, gas separation and collection systems, pressure regulation and storage equipment, and advanced control systems to monitor and optimize the entire process. At Superior Brands Corp., we specialize in delivering integrated SOEC solutions that harness the power of hydrogen as a clean and sustainable energy carrier.
-
SOEC Electrolysis: Pioneering Efficient Green Hydrogen Production
At Superior Brands Corp., we lead the way in high-temperature electrolysis solutions based on solid oxide cells, revolutionizing the production of green hydrogen. Our innovative approach integrates cutting-edge technology with sustainable practices to deliver efficient hydrogen generation for a cleaner future.
-
Elevating Hydrogen Production Efficiency
Our SOEC electrolyzer represents a breakthrough in hydrogen production by utilizing steam as the water feedstock, replacing the traditional liquid water. This unique approach allows us to intelligently harness waste heat from industrial processes, significantly reducing the demand for renewable energy sources to power the electrolyzer. By synergizing hydrogen production with waste heat recovery, we achieve unparalleled efficiency and sustainability.
-
The Science Behind SOEC Electrolysis
In the SOEC stack, water is introduced at the cathode, undergoing the water reduction reaction (WRR), which transforms water into hydrogen gas and oxide ions. The hydrogen gas is subsequently sent to purification modules for separation from residual water. Simultaneously, the oxide ions migrate from the cathode to the anode, releasing electrons to the external circuit, resulting in the formation of oxygen gas through the oxygen evolution reaction (OER). Operating within the temperature range of 700 to 1,000°C, SOECs benefit from high temperatures that facilitate the migration of oxide ions and enhance electrochemical reactions on both electrodes, leading to heightened overall efficiency.
-
Applications and Advantages
SOECs find ideal applications in industries such as oil refineries, steel manufacturing, and chemicals like fertilizer and ammonia production. These sectors require large amounts of hydrogen, and the integration of SOEC technology can result in significant cost savings and reduced carbon emissions. By utilizing steam feedstock and industrial waste heat, we ensure a sustainable hydrogen solution that aligns with the needs of energy-intensive industries.
-
Balancing Plant Components for Optimal Performance
Our SOEC plant is composed of meticulously designed components that ensure seamless operation and maximum efficiency:
• Water Treatment System (Reverse Osmosis and Electro-Deionizer): Thorough water treatment is essential for efficient electrolysis. Reverse osmosis and electro-deionization processes purify water, removing contaminants and impurities, ensuring high-purity water enters the SOEC stack. The water treatment system typically includes:
o Reverse Osmosis (RO): This process removes contaminants, ions, and impurities from the water by pushing it through a semipermeable membrane. RO helps achieve a high level of water purity by effectively filtering out dissolved solids and minerals.
o Electro-Deionizer (EDI): Electro-deionization further purifies the water by using an electric field to remove any remaining ions and impurities that may have escaped the RO process. This step ensures the water is highly purified and suitable for SOEC electrolysis.
• Heat Source Preparation: Our SOEC system requires water to be heated to the ideal temperature before entering the stack. We achieve this through various heat sources, such as industrial heat recovery steam generators (HRSG) or electric heaters. Common heat sources include:
o Industrial heat recovery steam generators (HRSG) Steam: Utilizing steam generated from external heat sources, such as concentrated solar power, waste heat from industrial processes, like refineries or ammonia production, to bring the water to the necessary temperature.
o Electric Heaters: Electrical heaters can also be used to heat the water to the desired temperature before it enters the SOEC stack.
• Solid Oxide Electrolyzer Cell (SOEC) Stack: The core of our SOEC plant, the stack, comprises interconnected SOEC cells that enable the electrolysis process. Operating at elevated temperatures, the stack facilitates the efficient conversion of steam into hydrogen gas and oxygen ions.
• Gas Separation and Collection: Efficient separation and collection systems ensure high-purity hydrogen output. Unlike other electrolysis methods, our SOEC process yields hydrogen with minimal impurities, simplifying the purification process. Typically, SOEC plants only require buffer tanks and dryers. These will usually be employed in between stages of compressors.
• Pressure Regulation and Storage: The hydrogen gas produced by the SOEC stack is initially at low pressure. Through multi-staged compressors and storage tanks, we elevate the gas pressure to suitable levels for storage and utilization.
At Superior Brands Corp., we specialize in delivering integrated SOEC solutions that harness the power of hydrogen as a clean and sustainable energy carrier. Our commitment to technological innovation and environmental responsibility drives us to pioneer efficient green hydrogen production for a greener and more sustainable world.